FROM DESIGN AND DEVELOPMENT
TO THE FINISHED MACHINE
//
Precise, custom-fit, efficient! HSK guillotine shears for production lines or stand-alone are consistently developed according to the individual requirements of our customers. Each guillotine shear is carefully designed, engineered and manufactured. Our products combine decades of experience and our unique know-how with energy-efficient and innovative cutting technology.
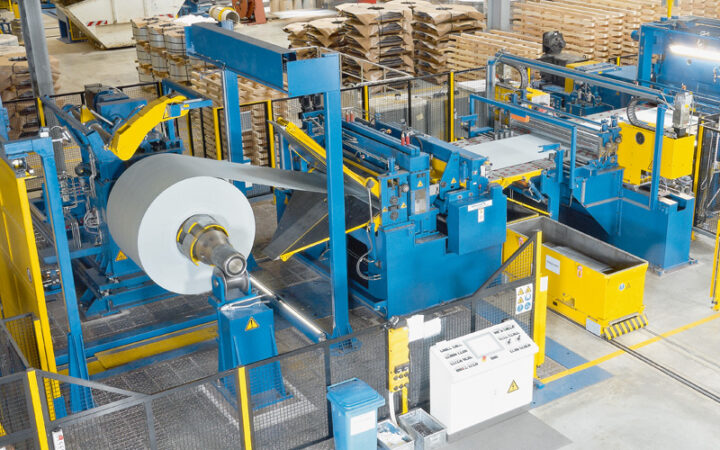
CUTTING SYSTEMS
Custom shears for automatic production lines.
Our high quality HSK-shears are often integrated with upstream or downstream machines to a fully automated production line. The machines are custom-designed and all the wishes of the customer are respected in the manufacturing of the shear.
The motor drive of the guillotine shear is also designed according to customer requirements and therefor realized using an AC gear brake motor, a servo gear motor or a flywheel with a pneumatically or hydraulically actuated clutch-brake combination.
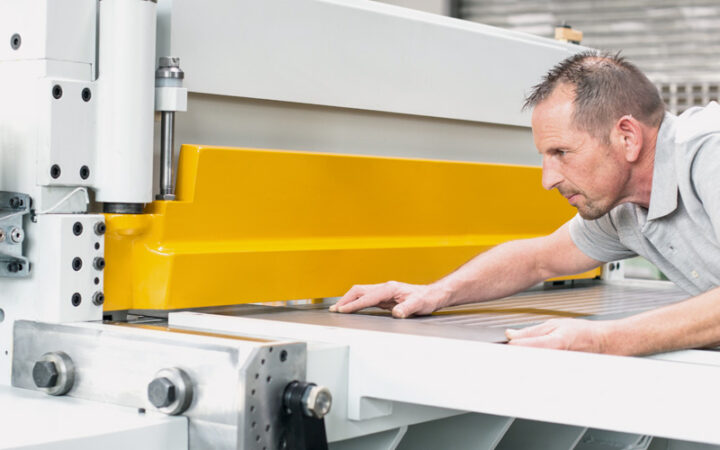
GUILLOTINE SHEARS
Individual, stand-alone shears for a wide range of materials.
HSK-guillotine shears are stand-alone, motor-driven machines with electrical control mostly used for cutting or trimming sheet metal.
It is also possible to cut other various materials like plastics, CFRP/GFRP, fleece material, foam or precious metals, mainly in form of sheets, but also formed work pieces like deep-drawing parts and profiled sheet metals, or directly from a coil.
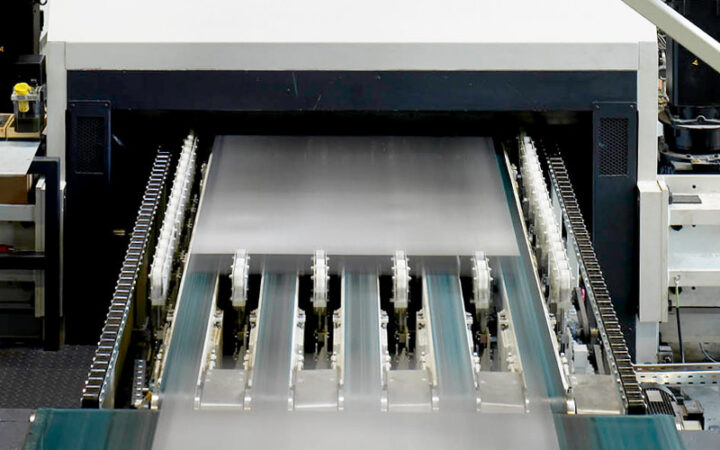
ENERGY EFFICIENT TECHNOLOGY
Cutting with the highest precision and minimal energy consumption.
In addition to their high precision, cutting speed and robustness, motor-operated eccentric shears from HSK are particularly characterized by a very high energy efficiency and environmental compatibility.
The disadvantages of hydraulically operated guillotine shears, such as the large amount of heat lost and the use of large quantities of hydraulic oil combined with a low number of strokes, are eliminated. Instead, the motor-operated drive of the HSK shears is designed individually for the customer’s specific task and is thus selected between the possible variants of AC geared motor, servo geared motor and clutch drive.
HIGH QUALITY SOLUTIONS
FOR ALMOST ALL REQUIREMENTS
Materials
The perfect cut for a wide range of materials.
HSK-cutting systems: coil / scrap web / sheet panel / electrical sheet / profiled sheet metal strip / needled aluminium / plastic strips / carbon filter mats / fleece mats / foam strips …
HSK-guillotine shears: sheet metal / welding gusset plates / perforated plate / expanded metal / copper cathodes / precious metals / circuit boards / plastics / rubber / foam material / corrugated cardboard / trapezoidal sheet …
OUR SERVICE
COMPLETELY CARE FREE
//
HSK is your reliable partner for quality guillotine shears. We offer you comprehensive services around our HSK machines and a competent service, such as maintenance, optimisations or all-round renewal.
ON-SITE SERVICES
Upon request, we can perform maintenance work on your HSK-machines on-site and take care of replacing wearing parts.
OVERHAULS
Transform old into new!
The eccentric shear will be dismantled into its component parts during the overhaul.
BLADE-SHARPENING
We would be happy to help you for re-sharpening or re-working of your shear blades.
CONTRACT PRODUCTION
The main expertise of our contract production team lies in a flexible production of components in small lot sizes.
LOCALLY GROWN
GLOBALLY KNOWN
//
3864+
realized shears
2680+
satisfied customers
108
years of experience
116
kWp installed PV system
2015 marks the centuriary year of HSK Engineering. In 1915 Karl Huttenlocher founded an engineering workshop in Kirchheim unter Teck, a picturesque village at the foot of the Swabian Jura in Baden Württemberg.
Five generations later, our company still operates as a typical Swabian family business – where roles and responsibilities are shared, and collaborative spirit exists between management and employees. Our approach to engineering combines innovative design with up-to-date technology and production standards of the highest order.
We are proud to look back on 100 years of continuous engineering development in which our machines have been and still are used by famous manufacturing companies around the world.
Whether it´s cars, washing machines, switch cabinets, transformers or even occlusal splints, our shears are a key part of the production process.
And they´re made by us – HSK Machine Engineering.
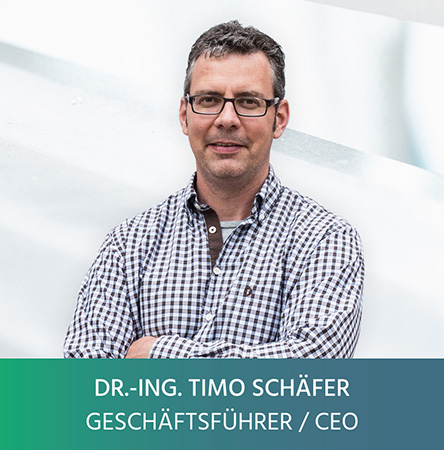
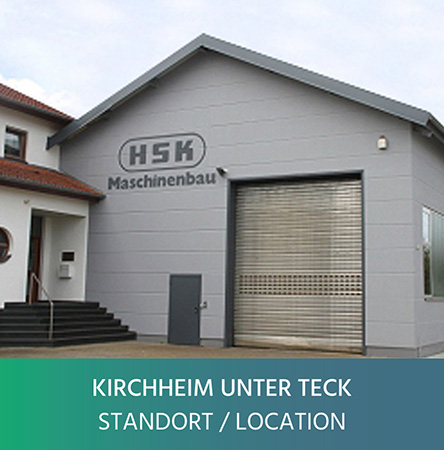
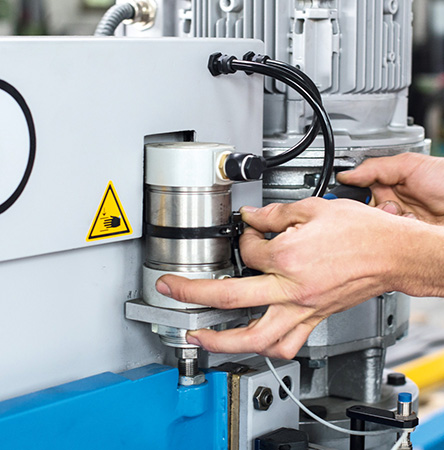
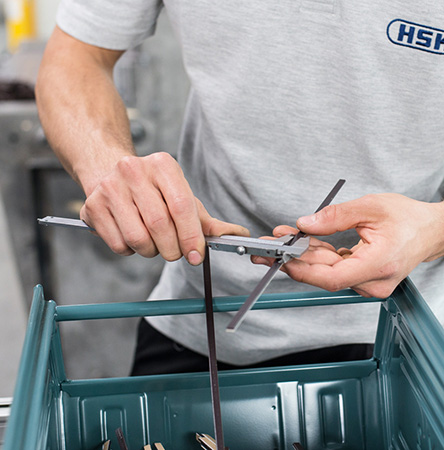
History
1915
Karl Huttenlocher founds an engineering workshop in Kirchheim/Teck.
1936
Production of the first mechanical guillotine shear.
1994
Manufacturing of the first guillotine shear for cutting corrugated and trapezoidal sheet metal.
1998
Manufacturing of the first mechanical guillotine shear with tandem drive for cutting sheet metal up to 15 mm.
2003
Manufacturing of the first double cutting shear with top-drive for cutting scrap web with a defined length.
2008
Installation of the first PV system on the roof of the factory with already 30 kWp.
2009
Manufacturing of the first cut-to-length shear with long-stroke construction with servo drive used as a swivel shear.
2013
Production of the first crop shear in a C-shaped frame.
2014
Manufacturing of the first twin shear with a combined cutter bar for disposing scrap web.
2014
Production of the first guillotine shear for cutting high trapezoidal profiles TP 100/275 and TP 135/310.
2015
Production of the first guillotine shear with 250 rpm for cutting scrap web behind a high-speed press.
2017
Production of the first guillotine shear for trimming two corners and sides of deep‑drawn components at the same time.
2017
First fine-cut guillotine shear for the automated cutting of Epstein samples particularly for quality control of electrical sheet metal.
2018
Production of the first strip steel shear for cutting Vulkollan and rubber with a thickness of up to 50 mm.
2022
Production of the first strip steel shear for cutting cellulolse insulation material for transformer production.
2022
Automation of the longitudinal slitting of roof profiles with a length of up to 7.5 m using a slitting shear.
2023
Production of the first guillotine shear for low-torsion cutting of titanium-nickel cathodes for chlorine gas electrolysis.
2023
Production of a high-end guillotine shear with an enlarged hydraulic clutch for cutting scrap web up to 80 releases per minute at a continuous stroke rate of 140 rpm.
2023
Expansion of the PV system on the roof of the factory to a total of 117 kWp for more self-sufficienacy and CO² savings
2024
Planned construction of the first bi-servo guillotine shear as flying shear integrated in a laser blanking line.
DO YOU HAVE QUESTIONS?
WE WILL BE GLAD TO HELP YOU.
CONTACT
We look forward to your call or message.
Do you have any questions about our products or would you like to make an appointment? We would be happy to get in touch with you.
Phone: +49 7021 59056 |
Email: info@hsk-maschinen.de |
Please note the privacy policy before sending your message.
The fields marked with * must be completed.
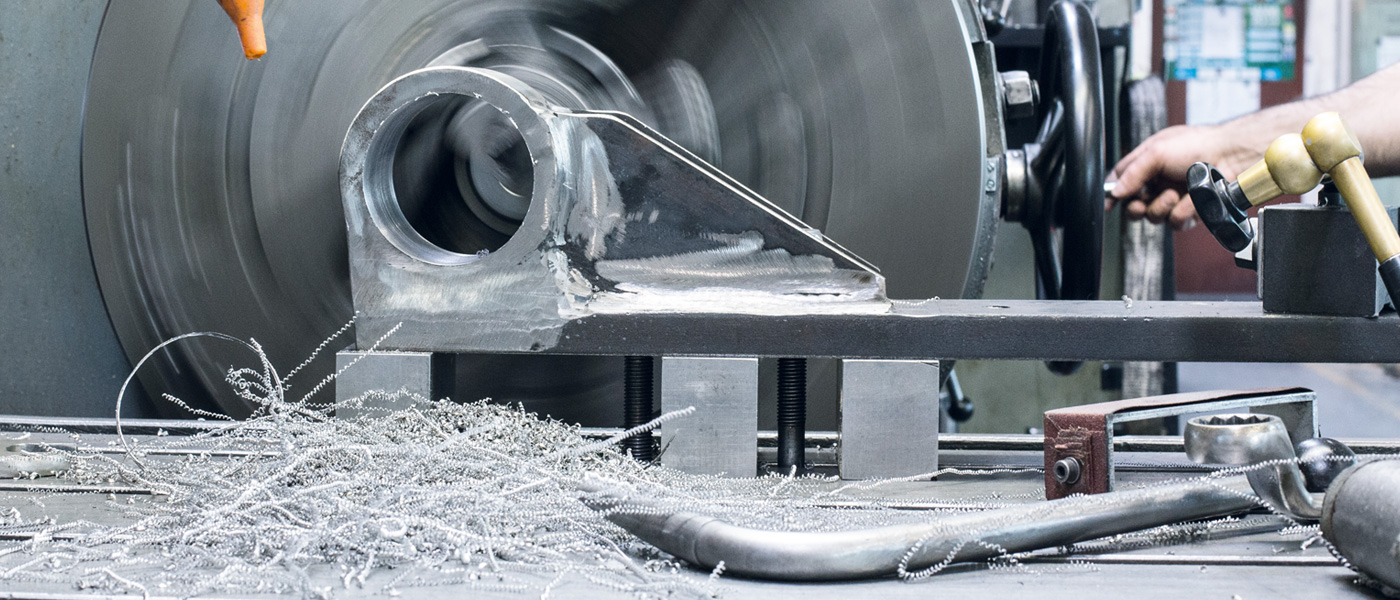