TECHNIK UND QUALITÄT
//
Die HSK-Maschinen werden bei uns im Haus mittels modernem 3D-CAD-System individuell konstruiert und anschließend nahezu komplett in unserem Werk gefertigt.
Vom Halbzeug bis zur fertigen HSK-Schere werden sämtliche Fertigungsschritte wie Schweißen, Schleifen, Fräsen, Hobeln, Drehen, Ausspindeln, Schaben, Spachteln, Lackieren und Montieren durchlaufen. Dabei besteht unser Team aus hochqualifizierten Fachkräften mit langjähriger Erfahrung. Darüber hinaus bilden wir seit Gründung der Firma kontinuierlich aus, um den qualifizierten Nachwuchs zu sichern.
Neben der Personalentwicklung liegt unser Fokus auf ständiger Erweiterung und Modernisierung der Produktionsstätte sowie den Fertigungsanlagen. So wurden in den vergangenen Jahren unter anderem größere CNC-Fräsmaschinen angeschafft und die Produktionsfläche durch einen neuen Hallenanbau um 50% erweitert.
ENERGIEEFFIZIENTE TECHNIK
Effizientes Schneiden optimiert für den jeweiligen Bedarf.
Bei HSK Scheren handelt es sich hauptsächlich um motorisch betriebene Exzenterscheren, welche durch Scherschneiden das zu zerteilende Material trennen. Hierbei wird ein schräg eingebautes, gerades Obermesser an einem geraden Untermesser vorbeibewegt und das Material abgeschert. Zur Einleitung der vertikalen Bewegung werden Exzenter verwendet, die mittels AC- oder Servo-Getriebemotor oder Kupplungsantrieb in Bewegung gesetzt werden.
Scheren mit Servoantrieb ermöglichen hierbei sehr effiziente Lösungen, insbesondere dann, wenn die Bremsarbeit in Kondensatoren zwischengespeichert oder ins Netz zurückgespeist wird oder an verkettete Maschinen wie z.B. einem Bandtreiber zur Verfügung gestellt wird. Aber auch Maschinen mit Schwungradantrieb erleben heute aufgrund Ihrer hohen Energieeffizienz eine Renaissance und sind bei vielen Anwendungen unter der zusätzlichen Berücksichtigung von Wirtschaftlichkeit und Robustheit modernen Servoantrieben überlegen.
Neben dem auf die Kundenanwendung exakt ausgelegten Antrieb, werden bei HSK auch sehr individuelle Lösungen realisiert, welche sich von der klassischen Exzenterschere unterscheiden. So wurden in der Vergangenheit folgende Sonderlösungen verwirklicht, welche das Feld der Trenntechnologie bei HSK entspechend erweitern:
Mit nach vorne gesetzter Exzenterwelle, damit geschnittene Tafeln senkrecht in der Schere nach unten fallen können.
Mit nach oben gesetztem Antrieb, wenn unterhalb störend (z.B. wenn sich dort ein Schrottcontainer befindet).
Mit Schwungrad-Direktantrieb für Dauerhubzahlen von bis zu 250 U/min. und häufigem Auslösen im Einzelhub.
Mit zwei eingebauten, parallelen Messerpaaren als Doppelschnittschere, um kleinere Schrottteile ermöglichen.
Mit zwei eingebauten, senkrecht zueinander verbauten Messerpaaren als Winkelschere, um Tiefziehteile zweiseitig zu besäumen.
In C-Bügel-Konstruktion, um entweder mit Material längs in die Schere oder die Maschine selbst von der Seite in die Linie einzufahren.
Als Bandstahlschere bzw. Leistenbandschere, um sowohl weiches Material wie Gummi oder Vukollan aber auch hartes Material wie Cellulose mit einem Bandstahlschnitt mit hoher Präzsion und Effizienz zu trennen.
Weitere Sonderlösungen wie z.B. das Längsteilen von 7,5 m langen Dachprofilen durch die Automatisierung einer Schlitzschere.
UNSER WEG ZU
HOCHWERTIGEN HSK-SCHEREN
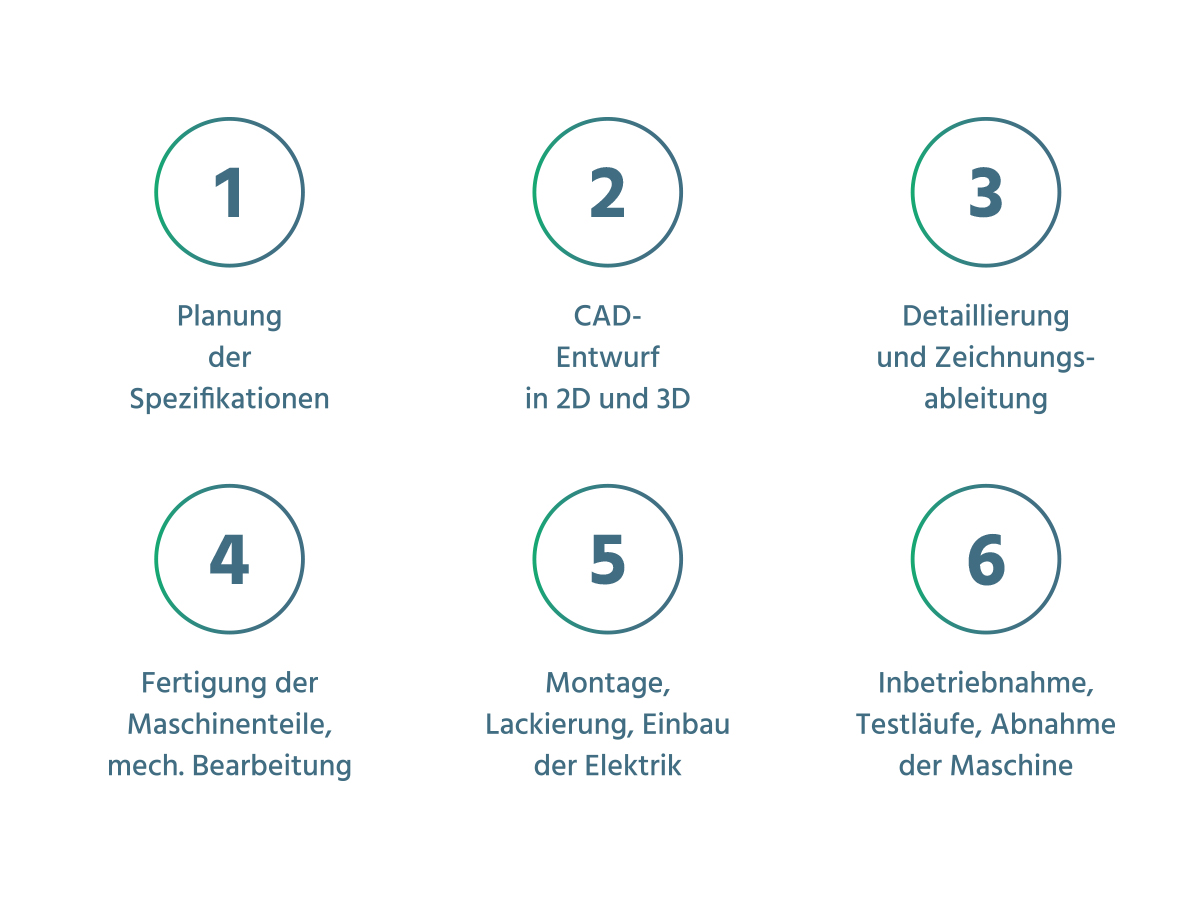
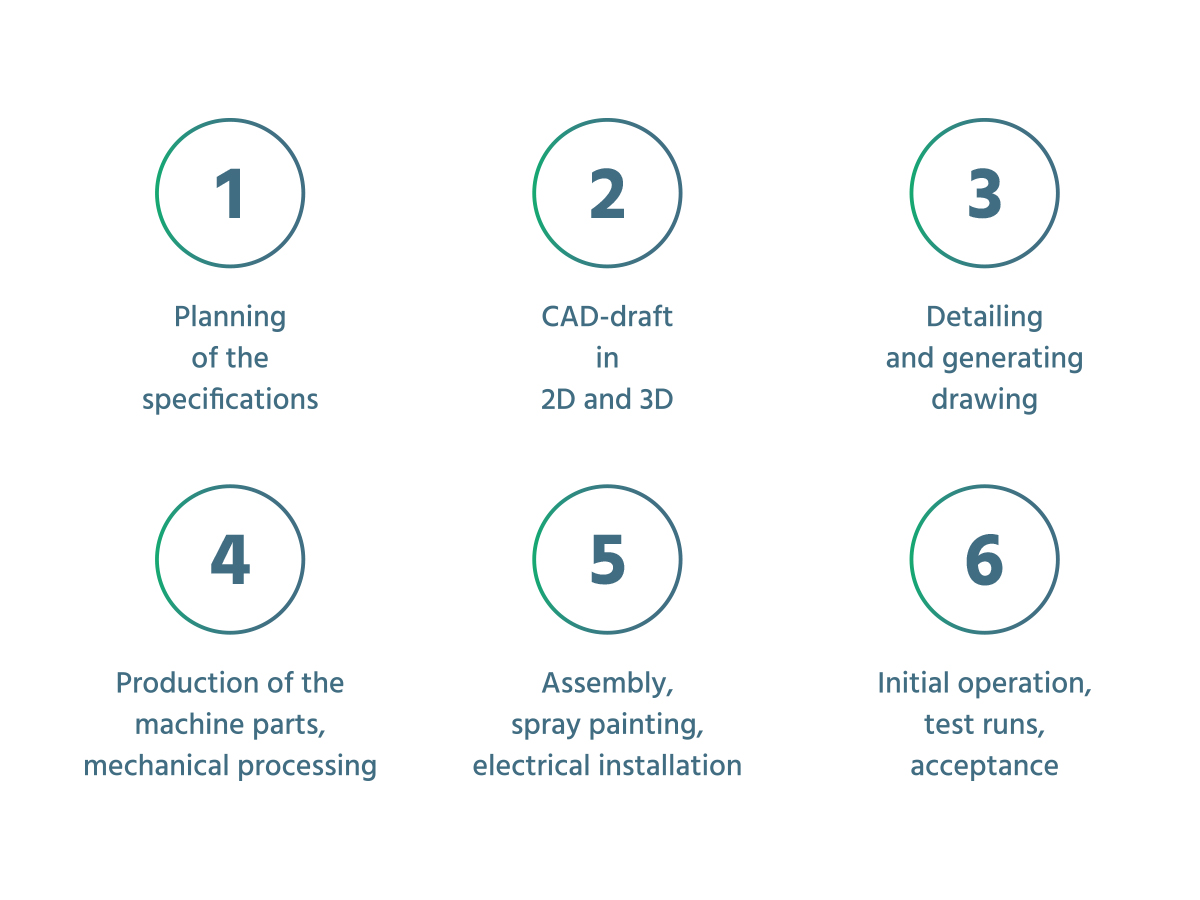
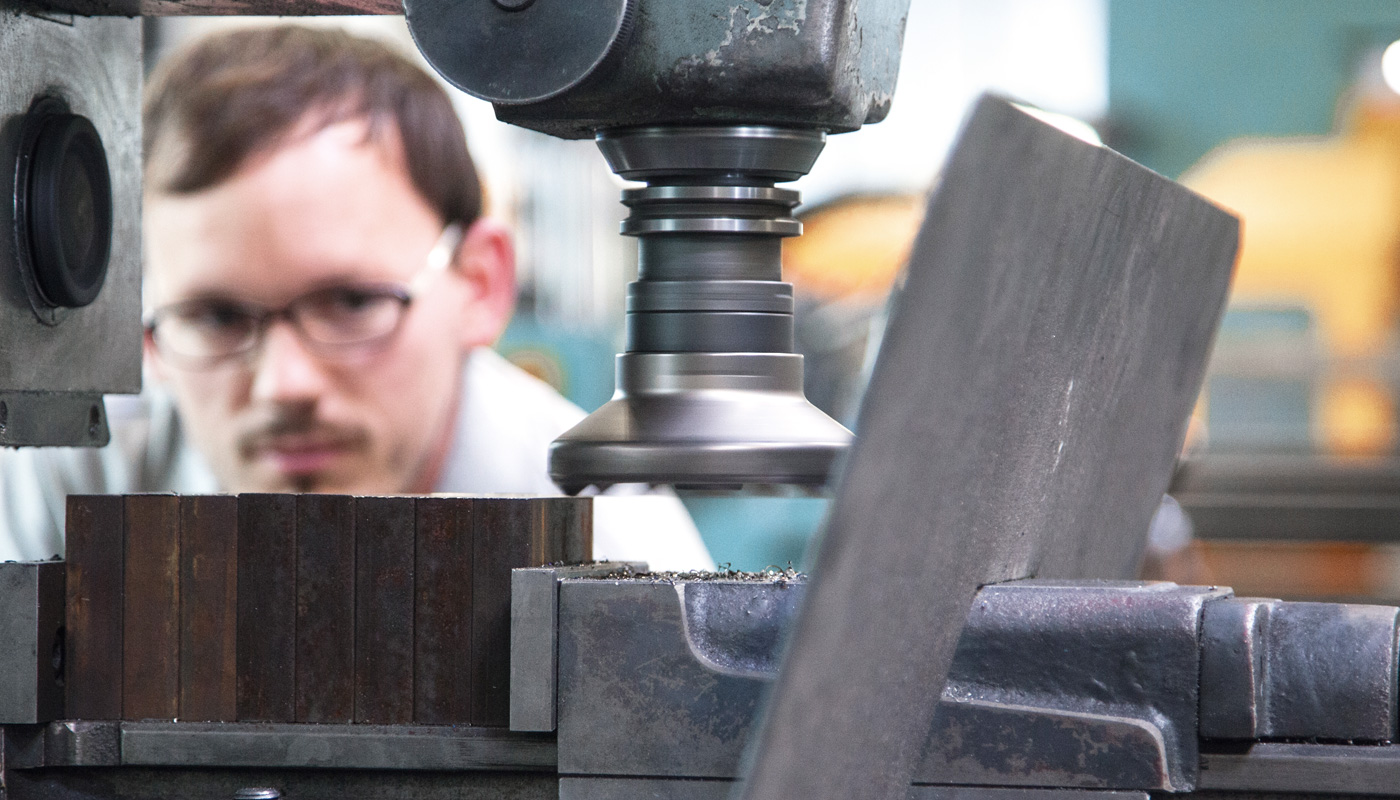
Referenzen
//
Namhafte Kunden in zahlreichen Branchen.
- 3A Composites
- Audi AG
- BAK Boysen
- Baosteel
- BAK Boysen
- BASF SE
- Bauknecht Hausgeräte
- Becker Stahl Service
- Beijing Benz Automotive
- Brose Fahrzeugteile
- Blanco
- BMW
- BSH Bosch und Siemens
- COGEBI Inc.
- Daimler
- Delta-Stahl
- ElringKlinger
- Faurecia
- Fiat
- Ford
- GEA Ecoflex
- Hörmann
- Indian Railways
- Johnson Controls
- Läpple Automotive
- Miele
- Neff
- Opel
- Oxford Automotive
- Quadrant Plastic Composites
- Schmitz Cargobull
- Shenyang Jinbei
- Stahlwerk Unna
- ThyssenKrupp
- VW
- ZF Friedrichshafen